A contactor is an electrical switch used for switching an electrical circuit on or off.
Table of Contents
contactor failure causes
A contactor is commonly used in various industrial and residential applications to control electric motors, lighting, heating elements, and other electrical loads. Contactors can fail for various reasons, and the causes of contactor failure may include:
- Electrical Overload:
- Overcurrent: Excessive current flowing through the contactor can cause overheating and damage to the contacts. This can be due to an overload on the connected equipment or a short circuit in the system.
- Mechanical Wear:
- Arcing and Pitting: Over time, repeated opening and closing of the contacts can lead to arcing and pitting, causing wear and deterioration of the contact surfaces. This can result in increased resistance and reduced contactor performance.
- Environmental Factors:
- Dust and Contaminants: Dust, dirt, and other contaminants can accumulate on the contactor’s contacts, affecting its performance and potentially leading to failure.
- Moisture: Exposure to moisture or humidity can cause corrosion on the contacts, leading to poor electrical conductivity and contactor failure.
- Poor Maintenance:
- Lack of Lubrication: Inadequate lubrication of moving parts within the contactor can result in increased friction, heat, and wear, leading to failure.
- Failure to Inspect: Regular inspection and maintenance are crucial to identifying early signs of wear or damage. Failure to conduct routine checks can lead to unexpected failures.
- Age and Usage:
- Normal Wear and Tear: As contactors age, they may experience normal wear and tear. Continuous usage can contribute to the deterioration of the contacts and other components.
- Improper Sizing:
- Undersized Contactor: If the contactor is not properly sized for the load it is controlling, it may experience excessive stress and overheating, leading to premature failure.
- Voltage Fluctuations:
- Voltage Spikes or Surges: Sudden increases in voltage can cause arcing and damage the contacts. Conversely, voltage drops can lead to welding of the contacts due to prolonged arcing during opening.
- Manufacturing Defects:
- Quality Issues: Poor manufacturing processes or the use of substandard materials can contribute to premature contactor failure.
- Incorrect Wiring:
- Incorrect Connection: Incorrect wiring or connection of the contactor can lead to improper functioning and failure.
- Harsh Operating Conditions:
- Extreme Temperatures: Operating in extremely hot or cold environments can impact the performance and lifespan of the contactor.
Regular maintenance, proper sizing, and adherence to manufacturer specifications are essential to prevent contactor failures.
Additionally, using protective devices such as fuses and circuit breakers can help mitigate some of the risks associated with electrical faults.
contactor failure symptoms
Contactors play a crucial role in electrical systems, and when they start to fail, certain symptoms may become apparent.
Recognizing these symptoms early can help prevent further damage to the contactor and the associated electrical components. Here are some common symptoms of contactor failure:
- Failure to Close or Open:
- Failure to Close: The contactor may not engage or close the circuit when the coil is energized.
- Failure to Open: The contactor may not disengage or open the circuit when the coil is de-energized.
- Excessive Noise:
- Unusual or excessive noise during the operation of the contactor, such as buzzing or humming, may indicate mechanical issues.
- Arcing:
- Visible sparks or arcs between the contacts during operation can indicate deterioration of the contacts.
- Burning Smell:
- A burning or overheated smell near the contactor may suggest excessive heat due to electrical resistance or mechanical issues.
- Intermittent Operation:
- The contactor may operate intermittently, causing erratic behavior in the connected equipment.
- Inconsistent Performance:
- Fluctuating performance of the contactor, such as intermittent failure to engage or disengage, can be a sign of impending failure.
- Increased Electrical Resistance:
- The resistance across the contacts may increase, leading to voltage drop and reduced current flow.
- Overheating:
- Excessive heat around the contactor, visible discoloration, or melting of insulation may indicate overheating issues.
- Visible Damage:
- Physical damage to the contactor, such as bent or burned contacts, indicates a problem.
- Excessive Contact Wear:
- Excessive wear on the contact surfaces, visible as pitting, arcing, or erosion, can be a sign of long-term deterioration.
- Failure to Handle Load:
- The contactor may fail to handle the specified load, resulting in equipment malfunctions or power disruptions.
- Failure to Energize Coil:
- If the coil does not energize or remains de-energized when power is applied, the contactor may not function properly.
- Abnormal Coil Sounds:
- Unusual sounds coming from the coil, such as clicking or buzzing, may indicate coil issues.
- Incorrect Timing:
- If the contactor does not operate with the expected timing, it may lead to coordination issues in the electrical system.
- Tripping of Protective Devices:
- If protective devices such as circuit breakers or fuses associated with the contactor trip frequently, it may indicate a fault.
If you observe any of these symptoms, it’s essential to investigate and address the issues promptly.
Regular maintenance, inspections, and testing can help identify contactor problems before they result in complete failure or damage to other components in the electrical system.
Contactor Maintenance
Regular maintenance of contactors is crucial to ensure their proper functioning and prevent unexpected failures. Here are some general guidelines for contactor maintenance:
- Visual Inspection:
- Regularly inspect contactors for any signs of physical damage, overheating, or discoloration. Check for loose connections and ensure that all parts are in good condition.
- Clean Contacts:
- Dust, dirt, and contaminants can accumulate on the contact surfaces, leading to increased resistance and potential failure. Clean the contacts using a soft brush or compressed air.
- Check for Wear:
- Inspect the contact surfaces for signs of wear, pitting, or erosion. If the contacts are significantly worn, consider replacing them.
- Tighten Loose Connections:
- Ensure that all electrical connections, including terminal screws and lugs, are tight. Loose connections can lead to overheating and increased resistance.
- Inspect Coil and Armature:
- Check the coil and armature for any damage or signs of wear. Ensure that the coil is securely in place and that there is no excessive wear on moving parts.
- Lubricate Moving Parts:
- If the contactor has moving parts, such as hinges or levers, lubricate them with an appropriate lubricant to reduce friction and wear.
- Check Control Circuits:
- Verify that the control circuits, including wiring and connections to the coil, are in good condition. Repair or replace any damaged wires or components.
- Verify Proper Sizing:
- Ensure that the contactor is appropriately sized for the load it is controlling. Undersized contactors can lead to overheating and premature failure.
- Check Voltage and Current:
- Measure voltage and current during operation to ensure that they are within the specified limits. Abnormal values may indicate a problem in the electrical system.
- Inspect Enclosure:
- If the contactor is housed in an enclosure, check for proper ventilation and cooling. Ensure that the enclosure is free from obstructions and contaminants.
- Test Operation:
- Test the contactor’s operation under normal conditions to ensure that it engages and disengages as expected. Verify the timing and coordination with other components in the system.
- Record Maintenance Activities:
- Keep a maintenance log that includes details of each inspection and any maintenance activities performed. This log can be valuable for tracking the contactor’s performance over time.
- Follow Manufacturer’s Guidelines:
- Adhere to the manufacturer’s recommendations and guidelines for maintenance. This may include specific intervals for inspection, cleaning, and replacement of components.
- Replace Worn or Damaged Parts:
- If any components, such as contacts or coils, show significant wear or damage, replace them promptly with parts recommended by the manufacturer.
- Consider Thermographic Inspection:
- Infrared thermographic inspection can help identify overheating issues before they cause a failure. Consider using thermal imaging equipment during maintenance checks.
By following these maintenance practices, you can help ensure the reliable operation of contactors and extend their lifespan.
Regular inspections and proactive measures can minimize the risk of unexpected failures in electrical systems.
what would cause a contactor to burn up?
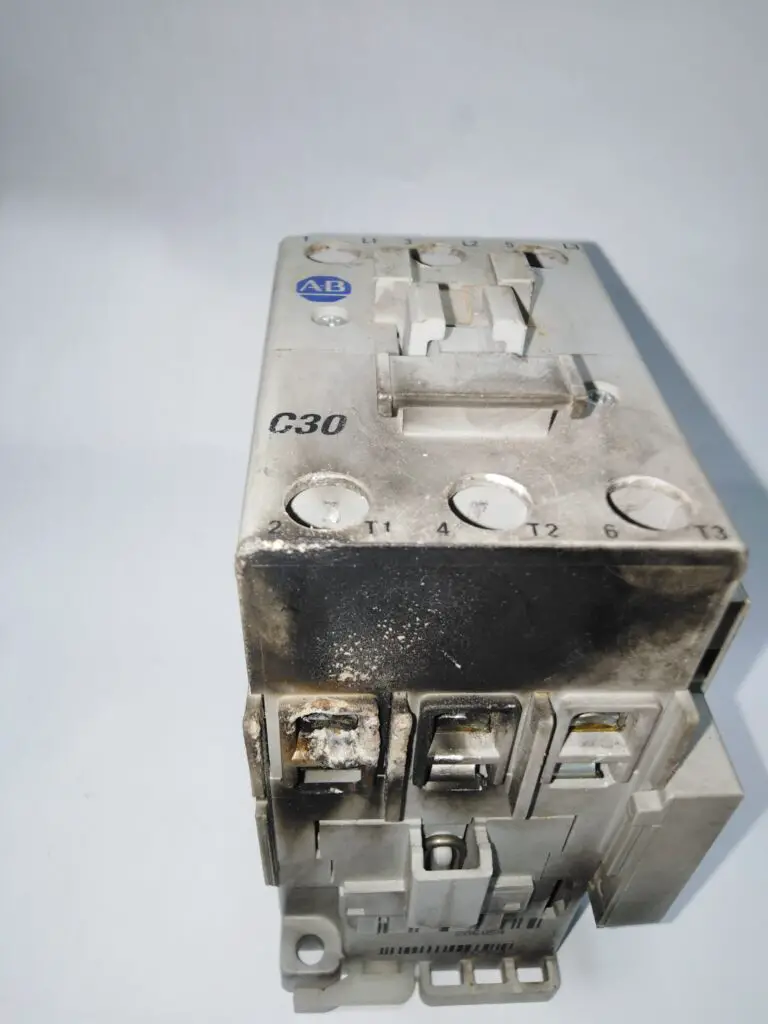
A contactor can burn up due to various factors, and it typically involves excessive heat generation, often caused by high currents, poor contact conditions, or other electrical issues. Here are some common reasons why a contactor might burn up:
- Overloading:
- Exceeding the rated current capacity of the contactor can lead to overheating. This can occur when the connected load is too large for the contactor or when there’s a fault in the system that causes a surge in current.
- Short Circuits:
- Short circuits in the electrical system can result in a sudden increase in current. If the contactor is not designed to handle such high currents, it can overheat and burn up.
- Poor Contact Surfaces:
- Deterioration of the contact surfaces due to wear, corrosion, or pitting increases electrical resistance. This elevated resistance generates heat during current flow, leading to overheating and potential burning of the contactor.
- Incorrect Sizing:
- Using a contactor that is undersized for the load it is controlling can result in continuous overloading, leading to overheating and burnout.
- Failure to Open Under Load:
- If the contactor fails to open the circuit properly when de-energized, it can lead to arcing between the contacts. Continuous arcing generates heat, which can cause damage and eventually result in burning.
- Voltage Spikes or Surges:
- Sudden increases in voltage, often caused by voltage spikes or surges in the electrical system, can lead to arcing and overheating within the contactor.
- Inadequate Cooling:
- Poor ventilation or cooling can contribute to overheating. Contactor failure may occur if it’s installed in an environment where it cannot dissipate heat effectively.
- Contaminants:
- Dust, dirt, or other contaminants accumulating on the contact surfaces can create additional resistance and contribute to overheating.
- Incorrect Wiring:
- Incorrect wiring or improper connections can cause increased resistance, leading to overheating and contactor burnout.
- Aging and Wear:
- Over time, contactors naturally experience wear and tear. Aging components, such as springs and contacts, may not function as efficiently, contributing to increased resistance and heat generation.
- Manufacturing Defects:
- Poor quality control during manufacturing can result in defects that compromise the contactor’s performance and lead to overheating.
- Lack of Maintenance:
- Inadequate or infrequent maintenance can allow issues such as worn contacts or poor connections to go unnoticed, increasing the risk of contactor failure.
When a contactor burns up, it is essential to investigate and address the root cause to prevent future failures.
This may involve replacing damaged components, ensuring proper sizing, improving ventilation, and addressing any issues with the electrical system.
Regular inspections and maintenance can help identify potential problems before they lead to catastrophic failure.
If there is uncertainty or if the issue is beyond the scope of your expertise, consulting with a qualified electrician is advisable.