I’m an electrical maintenance engineer, and my work revolves around keeping electrical systems running smoothly and safely. Our team handles a wide range of equipment, from low-voltage systems to medium-voltage machinery, ensuring everything operates at its best.
Our top priority? Preventing faults before they happen! We achieve this by implementing a well-structured preventive maintenance program, designed to catch potential issues early and keep downtime to a minimum.
Curious about what electrical maintenance really entails? Let’s dive in and explore the fascinating world of keeping the lights on and the machines humming!
Table of Contents
What is Electrical maintenance?
Electrical maintenance refers to the process of inspecting, testing, repairing, and servicing electrical systems and equipment to ensure they function safely, efficiently, and reliably. It is essential for preventing equipment failures, minimizing downtime, and maintaining safety standards in homes, businesses, and industrial settings.
Key Objectives of Electrical Maintenance:
- Ensure Safety: Prevent electrical hazards like shocks, fires, or equipment damage.
- Improve Reliability: Keep electrical systems running smoothly to avoid unexpected breakdowns.
- Extend Lifespan: Regular maintenance helps prolong the life of electrical components and systems.
- Optimize Performance: Ensure systems operate at peak efficiency, reducing energy waste.
Common Electrical Maintenance Activities:
- Visual Inspections: Checking for loose connections, damaged wires, or overheating.
- Cleaning: Removing dust and dirt from electrical equipment.
- Testing: Measuring voltage, current, and resistance to detect issues.
- Repairs: Fixing faulty components like switches, fuses, or circuit breakers.
- Upgrades: Replacing outdated systems to meet modern safety standards.
Electrical maintenance is vital in homes, commercial buildings, and industrial facilities to maintain safety, reduce energy costs, and ensure uninterrupted operation.
What do we need for electrical maintenance?
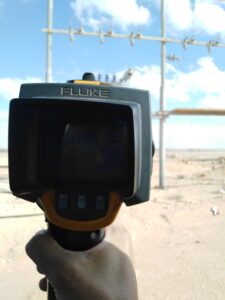
Alternatively, we might inquire, “What tools are essential for electrical maintenance?” In the course of my work, I rely on a variety of tools designed for electrical maintenance. Here is a list of some of the tools we use:
-
Hand Tools: These include cable cutters, insulated pliers, insulated screwdrivers, hacksaws, spanners, wire strippers, and hammers.
-
Measurement Devices: We utilize instruments like AVO meters, insulation resistance testers (megger testers), and grounding resistance measurement devices to assess electrical parameters.
-
Testing Devices: For testing purposes, we employ tools such as transformer oil breakdown voltage testers, circuit breakers and overload testers, and transformer turns ratio testers.
-
Additional Maintenance Equipment: This category encompasses equipment like transformer oil filtration units, thermal imaging cameras, and vacuum cleaners used for panel cleaning.
-
Maintenance Software: We also rely on computerized programs like MAXIMO and ORACLE maintenance to manage and organize our maintenance activities effectively.
These maintenance tools and equipment play essential roles in our electrical maintenance tasks. Each specific task may require a particular set of tools and devices, so it’s crucial to ensure you have the necessary equipment prepared before beginning any maintenance work.
Maintenance types
Electrical maintenance includes activities to ensure the safety, reliability, and proper operation of electrical systems. Here are common types of maintenance:
1. Corrective Maintenance
- What it is: Fixing or replacing equipment after it breaks or malfunctions.
- Example: Repairing a machine in a factory that stopped working unexpectedly.
- Pros and Cons: While straightforward, it can be costly and cause downtime.
2. Preventive Maintenance
- What it is: Scheduled inspections and servicing to avoid failures and prolong equipment life.
- Example: Regularly lubricating motor parts to prevent wear and tear.
- Pros and Cons: Reduces unexpected breakdowns but may involve unnecessary servicing.
3. Predictive Maintenance
- What it is: Using data and monitoring tools to predict when maintenance is needed, preventing failures.
- Example: Analyzing vibration data from a motor to determine when parts need replacement.
- Pros and Cons: Minimizes unnecessary maintenance but requires advanced monitoring tools.
4. Condition-Based Maintenance
- What it is: Real-time monitoring triggers maintenance based on the equipment’s actual condition.
- Example: Using thermal imaging to detect overheating in electrical panels and scheduling repairs.
- Pros and Cons: Reduces waste but depends on reliable sensors and systems.
Choosing the Right Approach
The choice depends on factors like:
- Equipment importance.
- Budget.
- Availability of monitoring technology.
- Safety requirements.
Best Practice: Combining multiple types of maintenance ensures reliability, reduces costs, and extends the lifespan of electrical systems.
Find out more details about Why Is Electrical Maintenance Important?
electrical maintenance work
Electrical maintenance involves tasks to keep electrical systems and equipment working safely and reliably. Here are some common tasks:
- Visual Inspection: Check for loose connections, damaged wires, or signs of wear and overheating.
- Cleaning: Remove dust and dirt to improve efficiency and prevent faults.
- Lubrication: Lubricate moving parts like motors to reduce wear.
- Testing and Measurement: Use tools to check voltage, current, and other parameters.
- Circuit Breaker Testing: Ensure breakers work properly to prevent overloads.
- Grounding Checks: Verify grounding systems to avoid shock hazards.
- Calibration: Adjust instruments for accurate measurements.
- Component Replacement: Replace worn or damaged parts like fuses or switches.
- Insulation Testing: Check cables for insulation issues to prevent short circuits.
- Thermal Imaging: Detect overheating spots in equipment.
- Power Quality Analysis: Monitor voltage stability and harmonics.
- Emergency Repairs: Fix failures quickly to minimize downtime.
- Safety Checks: Ensure devices like GFCIs and surge protectors are working.
- Documentation: Keep records of maintenance and repairs.
- Energy Efficiency Audits: Find ways to save energy and reduce costs.
- Upgrades: Modernize systems for better performance and safety.
- Software Maintenance: Update software for automation and control systems.
Regular maintenance is essential for homes, businesses, and industries to prevent failures, ensure safety, and extend equipment life.
Electrical maintenance work list
Certainly, here’s a table listing various electrical maintenance tasks:
Electrical Maintenance Task | Description |
---|---|
Visual Inspection | Visually examine equipment for signs of wear, damage, or loose connections. |
Cleaning | Remove dust, dirt, and contaminants from electrical components and connections. |
Lubrication | Apply lubricants to moving parts in electrical machinery to reduce friction and wear. |
Testing and Measurement | Measure electrical parameters like voltage, current, resistance, and capacitance. |
Circuit Breaker Testing | Test circuit breakers to ensure they function correctly in case of overloads or faults. |
Grounding and Earthing Checks | Verify that grounding and earthing systems are functioning correctly for safety. |
Calibration | Calibrate measuring instruments and sensors for accurate electrical measurements. |
Component Replacement | Replace damaged or worn-out components, including fuses, circuit breakers, and switches. |
Insulation Resistance Testing | Check the insulation resistance of cables and wires to prevent short circuits or electrical faults. |
Thermal Imaging | Use thermal imaging cameras to detect hot spots or overheating in electrical equipment. |
Power Quality Analysis | Monitor and analyze power quality parameters for a stable and reliable electrical supply. |
Emergency Repairs | Respond promptly to electrical system failures to minimize downtime and restore normal operation. |
Safety Checks | Ensure safety features like safety switches and GFCIs are functioning correctly for safety. |
Documentation | Maintain detailed records of maintenance activities, repairs, and inspections for reference. |
Energy Efficiency Audits | Identify energy efficiency opportunities and implement measures to reduce energy consumption. |
Upgrades and Modernization | Plan and implement upgrades to improve performance, safety, and compliance with standards. |
Software and Control System Maintenance | Maintain and update software programs and control systems for effective electrical management. |
These tasks are essential for the proper functioning and safety of electrical systems and equipment in various settings.
Don’t Leave Empty-Handed!
Install my Free Android App on Google Play:
Electrical Cables Most Common Tables “Cables Tables”
And, my Electrical Calculations App “Fast Electrical Calculator”
Discover more great content by subscribing to My channel
Looking to stay ahead of the game in the world of electrical engineering? Subscribe to my YouTube channel and gain access to exclusive content you won’t find anywhere else!
The staff I recommend
(Amazon Affiliate Links to products I believe are high quality):
- Economy 120 Volt/60Hz AC Power Source – Step-Down Voltage & Frequency Converters 1800W
- UNI-T Digital Multimeter Tester UT139C
- 50-Amp Extension Cord for RV “100ft”
- Voltage Stabilizer 110/220v
- Hair Dryer “best selling“
- TOSHIBA EM131A5C-BS Countertop Microwave Ovens
Disclaimer: This contains affiliate links to Amazon products. I may earn a commission for purchases made through these links.