Table of Contents
What does motor insulation Class mean?
Motor insulation class is a standardized system that categorizes the thermal tolerance of the insulation materials used in electric motors.
This classification is essential for ensuring the longevity and safe operation of the motor under various operating conditions.
Different motor applications require insulation systems that can withstand specific temperature ranges, which is why the insulation class is a crucial factor in determining the motor’s suitability for a particular environment.
The most common insulation classes are:
- Class A: Maximum temperature of 105°C
- Class B: Maximum temperature of 130°C
- Class F: Maximum temperature of 155°C
- Class H: Maximum temperature of 180°C
- Class C: A specialized class with a maximum temperature of 220°C
Why is Motor Insulation Class Important?
Motor insulation class is crucial for several reasons:
-
Temperature tolerance: Different motors operate at different temperatures, and the insulation class helps determine the maximum temperature a motor can handle before the insulation starts degrading. Operating a motor at a temperature higher than the specified insulation class can result in insulation failure, leading to reduced motor life or even motor failure.
-
Safety: Proper insulation ensures that the motor operates safely within the specified temperature range. Overheating due to inadequate insulation can lead to short circuits, electrical failures, and even fire hazards, which can endanger both the equipment and the surrounding environment.
-
Longevity and reliability: Insulation class directly impacts the longevity and reliability of the motor. Operating a motor within its specified temperature range ensures that the insulation remains intact and functional for an extended period, leading to reliable motor performance over its lifespan.
-
Efficiency: Maintaining the motor within its insulation class prevents overheating and energy losses. If the insulation fails, the motor might draw more current to compensate for the loss, leading to reduced energy efficiency and increased operational costs.
-
Compliance: Adhering to the appropriate motor insulation class is often a requirement for meeting industry standards and regulations. This ensures that the motor meets safety and performance standards set by regulatory authorities and industry bodies.
How to determine motor insulation classes?
Given a motor with insulation class F running at 110°C, the pertinent inquiry is whether this temperature is excessive.
In simple terms, this motor’s temperature is well within the acceptable range. Here’s the breakdown:
Referring to the NEMA insulation class table, the maximum Temperature Rise for this motor is 105°C. Factoring in the ambient temperature of 40°C yields 145°C.
Typically, the motor surface is approximately 30°C cooler than the winding temperature. Hence, the motor’s winding temperature here amounts to 110°C + 30°C = 140°C.
Consequently, the motor operates 5°C below its maximum Temperature Rise (145°C) and 15°C below its maximum permissible winding temperature (155°C). Thus, despite the temperature reaching 110°C, the motor is not excessively hot.
For a motor featuring an F class insulation, the temperature rise is 105°C + 40°C, leading to a total of 145°C at service factor 1. Given that F-class insulation can tolerate a maximum temperature of 155°C, this motor possesses a 10°C buffer.
Furthermore, if we encounter a motor with insulation class F and a temperature rise of B, denoted as F/B, it signifies a temperature rise of 80°C + 40°C, summing up to 120°C. Comparing this with the maximum allowable temperature of 145°C, the motor exhibits a surplus of 145°C – 120°C, equating to 25°C.
Motor Insulation Class A, B, F, and H
Major and most commonly used motor insulation classes include A, B, F & H. However, N, R, and S classes are also in use.
Class: A | 105 Degrees C |
Class: B | 130 Degrees C |
Class: F | 155 Degrees C |
Class: H | 180 Degrees C |
Before we dive into details, you should be aware of the following:
- NEMA allowable rise (maximum permissible winding temperature). This is the maximum temperature that the winding can handle.
- maximum temperature rise, This is the maximum temperature rise that the motor generates at full load and a certain service factor.
- Temperature margin (or hot spot Over Temperature), This is the subtract of NEMA allowable rise and Winding maximum temperature rise.
Class A:
When the ambient temperature near a Class A insulated motor is approximately 60 degrees Celsius, the motor can operate effectively without any issues.
However, surpassing this temperature threshold adversely impacts the motor’s performance. It’s crucial to ensure that the motor windings do not exceed 105 degrees Celsius.
A protective buffer of 5 degrees Celsius above the 105 degrees threshold is allowed.
For Class A motor insulation:
- The maximum permissible winding temperature is 105°C.
- The Maximum Temperature Rise is 60°C.
- A 5°C safety margin is permitted.
- Class A insulation commonly employs dielectric materials such as silk, cotton, or paper.
Class B:
Regarding Class B motor insulation, the motor can withstand temperatures of up to 130 degrees Celsius, while the ambient temperature can reach as high as 80 degrees Celsius.
In this class, a 10-degree margin beyond the temperature limit is permitted, enabling the activation of the cooling system until the temperature exceeds the limit by 10 degrees.
Here are the specifications for Class B motor insulation:
- Maximum permissible winding temperature: 130°C.
- Maximum Temperature Rise: 80°C.
- Allowed spot over 10°C.
Class B insulation materials commonly include glass fiber, mica, and asbestos.
Class E:
When considering Class E insulation, it’s important to note that the motor can tolerate temperatures up to 75 degrees Celsius in the surrounding environment.
In this class, the motor functions optimally when the ambient temperature is around 75 degrees Celsius. However, it’s crucial to ensure that the motor windings do not surpass 120 degrees Celsius. Similar to Class A, there’s a protective threshold of 5 degrees Celsius beyond the 105-degree limit.
This indicates that for Class E motor insulation:
- The motor can tolerate an ambient temperature of 75 degrees Celsius.
- The maximum permissible winding temperature is 120°C.
- There’s a protective buffer of 5 degrees Celsius, akin to Class A, beyond the 105-degree threshold.
Motor insulation Class F
In the case of Class F insulation, the insulation is capable of withstanding winding temperatures of up to 155 degrees Celsius. Meanwhile, the permissible ambient temperature can reach up to 80 degrees Celsius.
Within this class, a 10-degree margin above the temperature limit is allowed. This provides the flexibility to activate the cooling system until the temperature surpasses the limit by 10 degrees.
The key specifications for Class F motor insulation are as follows:
- Maximum permissible winding temperature: 155°C.
- Maximum Temperature Rise: 105°C.
- Allowed Hot-spot Over Temperature: 10°C.
Class F insulation comprises various dielectric materials such as mica, asbestos, and glass fiber.
Class H
Concerning Class H insulation, the insulation is designed to endure winding temperatures of up to 180 degrees Celsius, with an allowable ambient temperature range of up to 125 degrees Celsius.
In this class, a 15-degree margin above the temperature limit is permitted, providing the flexibility to engage the cooling system until the temperature exceeds the limit by 15 degrees.
The essential characteristics of Class H motor insulation include:
- Maximum permissible winding temperature: 180°C.
- Maximum Temperature Rise: 125°C.
- Allowed Hot-spot Over Temperature: 15°C.
Class H insulation often involves the use of silicon elastomers in combination with materials such as glass fiber and asbestos as the dielectric material.
Read my other detailed articles:
Which insulation class is better?
Determining which insulation class is better depends on the specific requirements of the application and the environmental conditions in which the motor will operate.
Each insulation class is designed to accommodate different temperature ranges and environmental constraints. Here’s a general perspective on each class:
-
Class A and B: These classes are suitable for applications with relatively lower temperature requirements. They are commonly found in light-duty applications and some household appliances.
-
Class E: This class offers better thermal endurance compared to Class A and B, making it suitable for applications where the motor is exposed to higher temperatures.
-
Class F: With a higher temperature tolerance compared to the previous classes, Class F is suitable for more demanding industrial applications where the motor is subjected to high temperatures and heavy-duty operations.
-
Class H: Providing the highest temperature resistance among the standard insulation classes, Class H is ideal for extremely high-temperature environments and heavy-duty industrial applications where motors are exposed to severe conditions.
The ‘better’ insulation class depends on the specific needs of the application. For instance, if a motor is operating in an environment with high temperatures, choosing a class with a higher temperature tolerance, such as Class F or H, would be more suitable.
However, selecting an insulation class that exceeds the requirements of the application might lead to unnecessary costs. It’s crucial to match the insulation class with the specific environmental and operational conditions to ensure optimal performance, longevity, and safety of the motor.
Every motor has its own range of temperature during its operation. This is called motor temperature rise.
The higher the difference between the motor rise and the insulation temp. the longer the motor life, but also the higher the price of the motor.
- allowable temperature rises at full load and 1.0 S.F.
A= | 60°C |
B= | 80°C |
F= | 105°C |
H= | 125°C |
- NEMA allowable temperature rises For a 1.15 S.F. motor
A= | 70°C |
B= | 90°C, |
F= | 115°C. |
NEMA Insulation Temperature Ratings | Motor Temperature Rises | ||||
1.0 SF | 1.15 SF | ||||
Insulation Class | Temperature | Ambient | Hots pots | Rise | Rise |
A | 105 | 40 | 5 | 60 | 70 |
B | 130 | 40 | 10 | 80 | 90 |
F | 155 | 40 | 10 | 105 | 115 |
H | 180 | 40 | 15 | 120 | — |
I have written a detailed article about How to megger a motor? Check it out.
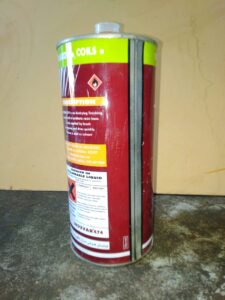
Motor Insulation Chart
Class | Maximum Operation allowance Degree Celsius | Maximum Operation Allowance Degree Fahrenheit | Allowable Temperature at Service factor 1.0 Degree Celsius | Allowable Temperature at Service factor 1.5 Degree Celsius |
A | 105 | 221 | 60 | 70 |
B | 130 | 266 | 80 | 90 |
F | 155 | 311 | 105 | 115 |
H | 180 | 356 | 125 | 115 and above |
For more details about, How does temperature rise affect electrical devices? Read my article.
motor insulation class for vfd
When selecting a motor insulation class for a Variable Frequency Drive (VFD) application, you need to consider the high-frequency voltage spikes and increased thermal stress caused by the VFD’s Pulse Width Modulation (PWM) output.
Recommended Insulation Class for VFD Motors
- Class F (155°C) or Class H (180°C)
- Class F insulation is commonly used for VFD-driven motors due to its ability to handle higher temperatures.
- Class H insulation provides an extra safety margin for extreme conditions.
- Inverter-Duty or VFD-Rated Motors
- These motors typically have Class F or H insulation with additional protection against voltage spikes and harmonics.
- They are designed to withstand higher dV/dt (rate of voltage change).
- Corona-Resistant Insulation
- Corona discharge can degrade insulation due to high-frequency voltage pulses.
- Motors designed for VFD applications often use enhanced winding insulation to resist premature failure.
Key Considerations for VFD Motor Insulation
- Voltage Rating: Motors should have insulation rated for at least 1600V peak to handle PWM waveforms.
- Thermal Overload: Use motors with a 1.15 service factor or better cooling systems.
- Bearing Protection: High-frequency currents can cause bearing damage, so consider insulated bearings or shaft grounding.
Read my article Motor Speed Formula And Calculator !
Conclusion
For VFD applications, Class F insulation (or better) with VFD-rated insulation enhancements is recommended. If operating in extreme conditions, Class H insulation may be a better choice. Always check motor manufacturer recommendations for compatibility with your VFD system.
Don’t Leave Empty-Handed!
Install my Free Android App on Google Play:
Electrical Cables Most Common Tables “Cables Tables”
And, my Electrical Calculations App “Fast Electrical Calculator”
Discover more great content by subscribing to My channel
Looking to stay ahead of the game in the world of electrical engineering? Subscribe to my YouTube channel and gain access to exclusive content you won’t find anywhere else!
The staff I recommend
(Amazon Affiliate Links to products I believe are high quality):
- Economy 120 Volt/60Hz AC Power Source – Step-Down Voltage & Frequency Converters 1800W
- UNI-T Digital Multimeter Tester UT139C
- 50-Amp Extension Cord for RV “100ft”
- Voltage Stabilizer 110/220v
- Hair Dryer “best selling“
- TOSHIBA EM131A5C-BS Countertop Microwave Ovens
Disclaimer: This contains affiliate links to Amazon products. I may earn a commission for purchases made through these links.